I think as these cobs continue to take over the grow light industry and the amount of DIY options available, doing it yourself is a great option but..... Safety first. Your dealing with electricity and not to scare anyone away but electricity is dangerous.
Hopefully this will be read by most diy'ers here and added to with tips and tricks to keep things spark free.
Below are some great ways to connect wires together. But I noticed that strand wire doesn't make as good of a connection in the push in connectors like these ideal push in connectors.
Or wago's which I do not have a picture of yet.
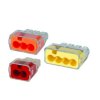
For strand wire I would recommend crimp caps like this type that can easily be crimped.
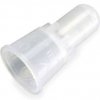
Also the ideal cob holders use the same type connection as the first photo. Again strand wire is ok but my personal opinion is using solid core wire makes a much tighter connection.
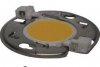
Hopefully this will be read by most diy'ers here and added to with tips and tricks to keep things spark free.
Below are some great ways to connect wires together. But I noticed that strand wire doesn't make as good of a connection in the push in connectors like these ideal push in connectors.
Or wago's which I do not have a picture of yet.
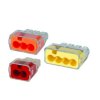
For strand wire I would recommend crimp caps like this type that can easily be crimped.
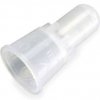
Also the ideal cob holders use the same type connection as the first photo. Again strand wire is ok but my personal opinion is using solid core wire makes a much tighter connection.
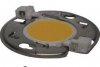
Last edited: