DIY- How to build an essence oil extractor that will safely produce highly concentrated THC oil
DIY- How to build a boiler for the essence oil apparatus.
DIY- How to process buds that will be used in said extractor.
I assume that if you are growing your own medicine, you are a DIY type person. I would like to share some ideas regarding safely producing your own THC oil concentrate. If I were to rate the difficulty of this project, I would rate it moderate/high. The main reason it is challenging is that it requires working with copper and stainless and having the ability to solder these metals together. To be blunt, it can be extremely dangerous if you do not take care and learn every aspects of properly building and running such an apparatus.
Some basic common sense before attempting:
You will be building something that is designed to boil alcohol and water producing vapor. Vapor is a gas, and this gas will continue to be produced so long as an adequate heat source is applied. Meaning, gas will expand and fill an enclosed space building up pressure. This will continue until something gives. A seal might break, or the entire apparatus might explode. You never build something that closes itself off to the environment. You always have it vented. If you do not understand every aspect of the apparatus, do not build it.
Alcohol is an amazing solvent. It is good at dissolving many things. It will dissolve THC oil and it will also dissolve many synthetics. You should NEVER use synthetics in the construction of your apparatus. Silicone, plastics, rubber are ALL out of the question. Here are 4 things that can come in contact with alcohol and is considered safe: Copper, Stainless steel, lead free solder, Teflon. Using synthetics while working with 95.5% alcohol at high temperatures will leach nasty things into your final product. You can go on youtube and find many people using plastics in producing their Ethanol THC oil and it should make you cringe. The only synthetic that I know that has been shown to be safe is Teflon. Teflon appears to not react to alcohol even at high temperatures.
NEVER boil high percentage alcohol anywhere near an open flame. No smoking near high percentage alcohol. You will be boiling this stuff and it is roughly the same as boiling gasoline.
You should use this outside.
NEVER run your apparatus unattended.
Some building skills you will be utilizing:
Drilling, grinding, and cutting copper and stainless
Soldering copper to copper, Soldering copper to stainless
You should be able to purchase everything for the essence oil apparatus at the big box stores, like homedepot/lowes; the copper, solder, and various tools etc. You will need to purchase a special type of flux that is capable of allowing you to join copper to stainless.
The apparatus: This is essentially a still head. It is fitted above the boiler and its job is to convert the vapor back to liquid so that it can be safely collected. You will find many people forgo this step because they lack the knowledge/desire and are ok with letting the alcohol vapors escape to the environment. I think this is dangerous and wasteful. I recommend using a food grade alcohol such as 191everclear. This is not cheap, so you will want a way to collect and reuse it.
My favorite apparatus to construct is called a concentric still head. This is compact and relatively easy to construct. This is a one inch design allowing for less expensive materials to be used. The copper tube can be found at homedepot as well as all the copper fittings. Copper is not cheap, but you should be able to put this together for roughly 60 u.s. dollars. I am going to do my best to provide a parts list within a diagram.
Here is an over simplified explanation of how this apparatus works. The name concentric means ring inside a ring. The outer most ring is the outside of the water sleeve. Water flows between this outer sleeve and an inner sleeve. This is what rapidly cools off the vapors as they try to escape out of the VENTED top of the apparatus. You want this water coming from a cool source. Ok, so far we have an outer tube and an inner tube of copper, between these two tubes water is flowing; I connect an intake from my sink's water sprayer - I then connect a drain line that dumps back into the sink. So imagine the vapors boiling out of your boiler, they are rising up and being cooled off and converted back into liquid. The apparatus has another tube on the inside that creates a well where the liquid (alcohol distillate) collects. A take-off 1/4 inch tube drains this well so that you can collect it. You will run a 1/4 inch copper tube back to a collection vessel. This is how you will reclaim your alcohol. Essentially, you are collecting your alcohol solvent to be reused -- boiling off the solvent leaves behind the THC oil that you are making. Here is a picture so that you have a basic idea.
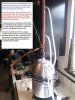
This is an overview. I plan to reserve 3 Posts after this one and fill them in with detailed information. Please know that I consider this an essence extractor. Your state/country may consider it a still. Construction and/or operating such a thing could be illegal! If the moderators do not wish me to post this, I completely understand...so feel free to delete this post. Heck, I am not sure people on this forum is interested in such things. I do know that a lot of people are producing Ethanol THC-oil in dangerous ways. I figure adding my 2cents wouldn't hurt.
DIY- How to build a boiler for the essence oil apparatus.
DIY- How to process buds that will be used in said extractor.
I assume that if you are growing your own medicine, you are a DIY type person. I would like to share some ideas regarding safely producing your own THC oil concentrate. If I were to rate the difficulty of this project, I would rate it moderate/high. The main reason it is challenging is that it requires working with copper and stainless and having the ability to solder these metals together. To be blunt, it can be extremely dangerous if you do not take care and learn every aspects of properly building and running such an apparatus.
Some basic common sense before attempting:
You will be building something that is designed to boil alcohol and water producing vapor. Vapor is a gas, and this gas will continue to be produced so long as an adequate heat source is applied. Meaning, gas will expand and fill an enclosed space building up pressure. This will continue until something gives. A seal might break, or the entire apparatus might explode. You never build something that closes itself off to the environment. You always have it vented. If you do not understand every aspect of the apparatus, do not build it.
Alcohol is an amazing solvent. It is good at dissolving many things. It will dissolve THC oil and it will also dissolve many synthetics. You should NEVER use synthetics in the construction of your apparatus. Silicone, plastics, rubber are ALL out of the question. Here are 4 things that can come in contact with alcohol and is considered safe: Copper, Stainless steel, lead free solder, Teflon. Using synthetics while working with 95.5% alcohol at high temperatures will leach nasty things into your final product. You can go on youtube and find many people using plastics in producing their Ethanol THC oil and it should make you cringe. The only synthetic that I know that has been shown to be safe is Teflon. Teflon appears to not react to alcohol even at high temperatures.
NEVER boil high percentage alcohol anywhere near an open flame. No smoking near high percentage alcohol. You will be boiling this stuff and it is roughly the same as boiling gasoline.
You should use this outside.
NEVER run your apparatus unattended.
Some building skills you will be utilizing:
Drilling, grinding, and cutting copper and stainless
Soldering copper to copper, Soldering copper to stainless
You should be able to purchase everything for the essence oil apparatus at the big box stores, like homedepot/lowes; the copper, solder, and various tools etc. You will need to purchase a special type of flux that is capable of allowing you to join copper to stainless.
The apparatus: This is essentially a still head. It is fitted above the boiler and its job is to convert the vapor back to liquid so that it can be safely collected. You will find many people forgo this step because they lack the knowledge/desire and are ok with letting the alcohol vapors escape to the environment. I think this is dangerous and wasteful. I recommend using a food grade alcohol such as 191everclear. This is not cheap, so you will want a way to collect and reuse it.
My favorite apparatus to construct is called a concentric still head. This is compact and relatively easy to construct. This is a one inch design allowing for less expensive materials to be used. The copper tube can be found at homedepot as well as all the copper fittings. Copper is not cheap, but you should be able to put this together for roughly 60 u.s. dollars. I am going to do my best to provide a parts list within a diagram.
Here is an over simplified explanation of how this apparatus works. The name concentric means ring inside a ring. The outer most ring is the outside of the water sleeve. Water flows between this outer sleeve and an inner sleeve. This is what rapidly cools off the vapors as they try to escape out of the VENTED top of the apparatus. You want this water coming from a cool source. Ok, so far we have an outer tube and an inner tube of copper, between these two tubes water is flowing; I connect an intake from my sink's water sprayer - I then connect a drain line that dumps back into the sink. So imagine the vapors boiling out of your boiler, they are rising up and being cooled off and converted back into liquid. The apparatus has another tube on the inside that creates a well where the liquid (alcohol distillate) collects. A take-off 1/4 inch tube drains this well so that you can collect it. You will run a 1/4 inch copper tube back to a collection vessel. This is how you will reclaim your alcohol. Essentially, you are collecting your alcohol solvent to be reused -- boiling off the solvent leaves behind the THC oil that you are making. Here is a picture so that you have a basic idea.
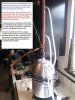
This is an overview. I plan to reserve 3 Posts after this one and fill them in with detailed information. Please know that I consider this an essence extractor. Your state/country may consider it a still. Construction and/or operating such a thing could be illegal! If the moderators do not wish me to post this, I completely understand...so feel free to delete this post. Heck, I am not sure people on this forum is interested in such things. I do know that a lot of people are producing Ethanol THC-oil in dangerous ways. I figure adding my 2cents wouldn't hurt.